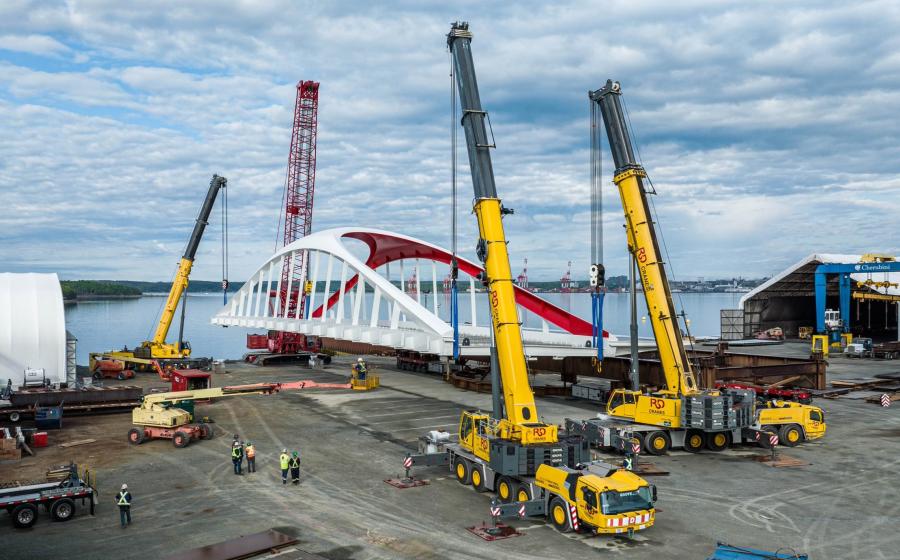
Mon October 10, 2022
Manitowoc
Canada's Cherubini Bridges and Structures has completed work on the Four Signature Bridges contract for Toronto's Port Lands project.
The job wrapped up in style with the company successfully orchestrating a complex four-crane pick to get the final 492 ton segment of the bridge sent up the St. Lawrence River by barge.
The lift of the 73 ft.-wide, 187 ft.-long Cherry Street North Bridge was performed by R&D Crane which — like the fabricator — is a division of Cherubini Group. It was completed using the four largest cranes in its fleet: a Manitowoc Model 16000 lattice-boom crawler, and Grove GMK6400, GMK5250L and GMK5240 all-terrain models.
The cranes combined to lift the structure from its supports in the yard at Cherubini's Pleasant Street Fabrication Facility in Dartmouth, Nova Scotia, allowing a self-propelled modular transporter (SPMT) with transfer beams and a huge Cherubini-engineered turntable to take the load. The SPMT was then driven onto a barge moored alongside the site's dedicated harborside wharf to begin its journey to Toronto.
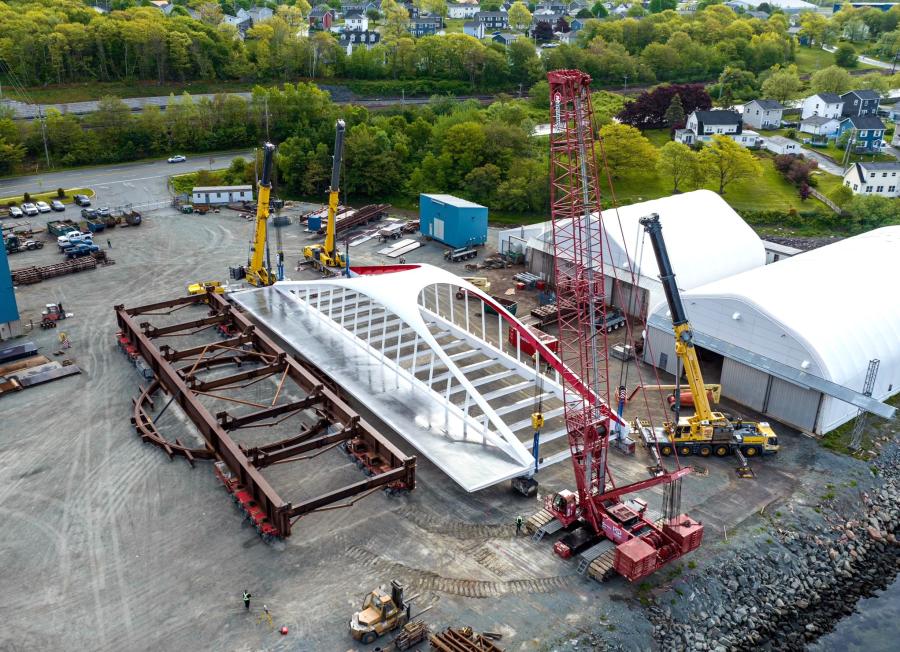
Finding Room in a Tight Spot
The need to bring together the four cranes was an engineering solution to help ensure the bridge was positioned as smoothly as possible at its final resting place, as Cherubini Group CEO, Darren Czech, explained.
"Loading the bridge sections onto the barge wasn't the issue, as the transporters were able to pick the sections and drive straight on," he said. "But with this particular section, and also a second one, there were space restrictions which meant we couldn't just simply roll on and roll off the barge using the self-propelled transporters alone.
"Because of the this, we engineered a solution that supplied the sections to the job site on a turntable structure — our giant ‘Lazy Susan.' This allowed tugboats in Toronto to spin them around on the barge in the middle of the harbor, ideally positioning them to slot right into their final resting place. So, we used the four-crane pick at our yard to make sure the section was accurately placed on the turntable ahead of shipping to Toronto."
For the lift, one crane was positioned at each corner of the bridge, and all were configured with main boom and partial counterweight. The 16000 had 118 ft. of boom with 148 ton of rear counterweight and 30 ton of carbody counterweight. All three Groves maximized their outrigger deployment, with the GMK6400 working with 105 ton counterweight and 65.6 ft. of boom; the GMK5250L working with 77 ton counterweight and 77 ft. of boom; and the GMK5240 working with 48.5 ton counterweight and 75.5 ft. of boom.
"The lift went without a hitch, taking less than four hours," said R&D's GM, Rob Blois. "Although the cranes were mobilized roughly a week prior to help with planning, setting up mats, and finalizing onsite details.
"The key was really the planning — working out how to maintain equal weights during the lift and spreading the load to reduce ground-bearing pressure. But on the day the cranes worked very well together. We have a full fleet of Manitowoc and Grove machines, which minimizes the mechanical and operational challenges a mixed fleet can cause."
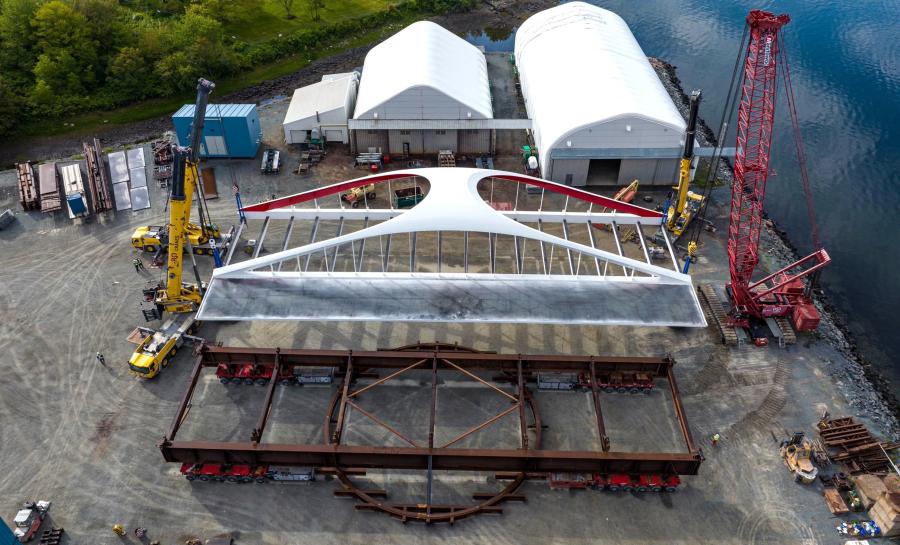
The personnel also played a key role in ensuring the job was performed safely and effectively, added Czech:
"The supervisor facilitating the lift, Nico Baldasso, had previously operated all the cranes himself, so he recognized and understood how each crane should perform. And, of course, we always use the right operator for the right crane.
"Pretty much every bridge that's erected in this province is done by us — we embrace the big and bulky stuff that other people don't want. So multi-crane picks are not unusual to us or our operators. They're like a hockey team that's been playing together a long time; they can predict each other's moves so Nico can oversee the work and just let them get on with the job."
Final Piece of Puzzle
The final key player in the project is local Manitowoc dealer Shawmut Equipment — located in nearby Elmsdale, Nova Scotia — Cherubini's preferred partner ever since it started building its crane fleet. From its convenient location in nearby Halifax, Shawmut provides expeditious service that Czech described in glowing terms:
"It really is a team effort, and we value the intimate knowledge the Shawmut team has of these cranes and the relationships they build with our operators. One of Shawmut's many technicians, Michel Landry, is a great resource and has walked our operators through many issues. He does it so well, no one but the operator even knows there's been a snag. That expertise is phenomenal.
"And we can't do it without their sales rep, Dave Hawboldt or Joe Vergoni, the president — I can pick up the phone any time and ask them anything. It's a real family-like partnership."
For more information, visit www.manitowoc.com.