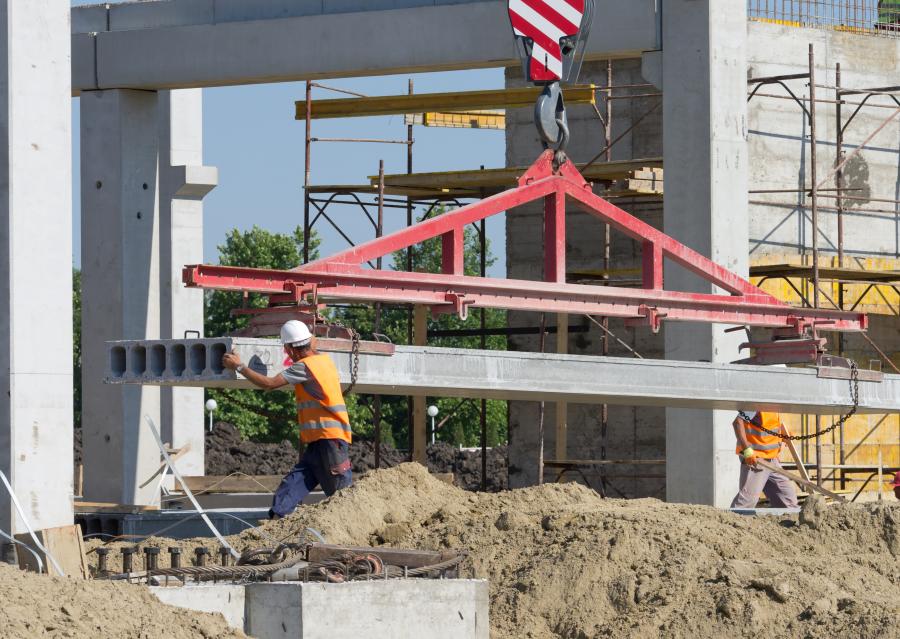
Mon April 17, 2023
Lucy Perry – CEG CORRESPONDENT
Installing a below-the-hook lifting device can streamline a lift and ensure the safety of your crew and the load. The device is used to attach a load to a crane so the load can be moved safely and may involve slings, hooks and rigging hardware. The idea behind below-the-hook spreader bars and lifting beams is to minimize the potential for damage to the load, other rigging hardware and personnel on the ground.
Custom-built below-the-hook devices are very common, according to rigging gear provider Mazzella Companies.
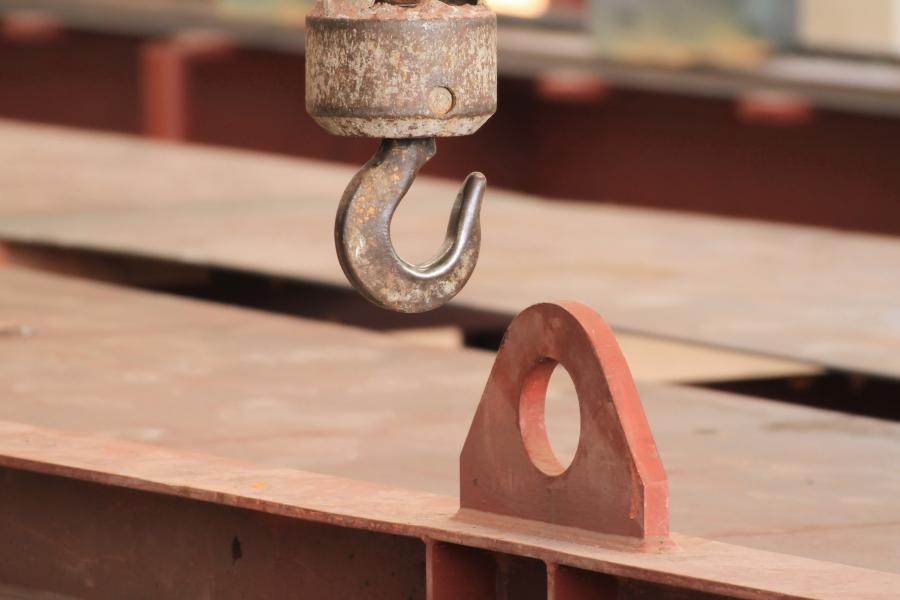
"Engineered lifting devices are built for picking and moving a load due to its size, shape or center of gravity," the company blogged. "A manufacturer will partner with their customer to develop a completely new device from scratch."
They may, instead, modify an existing product design for specific lifting needs. Most manufacturers also carry standard sizes and configurations for common applications, such as lifting and moving pipes or bars.
With these tools, coils and horizontal materials can be stacked and pallets and structural shapes can be moved.
"Below-the-hook lifting devices are most often mechanical, but can also be operated electronically, hydraulically or pneumatically."
Special controls are engineered into the design of the product to operate claws, tongs, hooks or latches, said Mazzella.
Though they appear similar, spreader bars and lifting beams cannot be used interchangeably. Their differences can make or break a lift.
Protecting Load, Crew
"These two devices are not interchangeable," said engineers at Holloway Houston Lifting (HHI), Houston, Texas.
Spreader bars and lifting beams stabilize and support loads, and both are used to keep slings perpendicular to the horizon while moving. According to the HHI website, these below-the-hook lifting devices are still misunderstood.
They "are significantly different in both appearance and by functional definition," said Bob Kozickie, technical sales support manager, Peerless Industrial Group. "Industry slang terminology, however, creates a semantics error, often mistaking which lifter is required on the job by calling both a ‘spreader beam.' There is a distinct difference between the two which can be explained by examining both beam styles."
Lifting With Ease
Lifting beams attach directly to the crane or hoist hook and deflection occurs outward from the center, Kozickie blogged.
The strength when lifting is derived from the beam material and configuration. Lifting beams can be manufactured from round or square tube, channel or I-beams, he added. As the device increases in capacity, I-beams become the dominant steel required to attain the higher working load limits.
"Lifting beams are often supplied with multiple pick points, which provide adjustability based on load configuration and center of gravity."
The lifting beam's design offers a low center connection to the hoist hook for areas where headroom is a major concern. They can be engineered as low headroom devices that are often required for critical lifts.
Potential lifting beam configurations can be as simple as a triangular short span with two lifting points one foot apart. They can be a complicated four-point adjustable lifting beam with multiple pick points. They also can be used with a single crane or synchronous dual cranes, if required.

"Spreader beams require top rigging to support the load," said Kozickie. "The triangular configuration forces the beam to lift with compression on itself rather than the deflection that occurs with a lifting beam."
This condition creates a slight advantage to using the spreader bar over a lifting beam in that it provides much more stability, he said.
When using a lifting beam, the load must be centered exactly under the crane hook to attain a level lift. The spreader bar does not require that the center of gravity be as exact.
"The extra top rigging also exemplifies the fact that a greater amount of headroom is needed to lift and transport the load," Kozickie said.
Although lifting beams appear as simple a device as a spreader bar, they are different in design.
"A lifting beam has a single attachment point in the center of the beam — not just two attachment points on the ends for slings," said HHI. "This allows the lifting beam to connect to a crane/hoist, then support the load via hook or rigging sling."
Ideally, lifting beams are used for lighter loads in short periods, providing multiple lifting points, according to the Houston, Texas, company. These devices can be designed to fit specific applications and/or projects.
The best application for a lifting beam is when moving off-balanced loads or trying to control inward crushing forces. They're also designed specifically for use with special load-securement attachments.
Lifting beams are not meant to be used when a lightweight device is called for. They are rigid and heavy, said HHI. A lifting beam is the wrong tool in applications where the load has a wide span that requires significant lifting, said the company. They're also the wrong choice when there's a concern about the load tipping or spinning.
Spreading the Load
A spreader bar has limited configurations available to the rigger. Spreader bars can be fixed or adjustable. They also can consist of square or round tubing in a box style spreader beam design.
"End cap spreader beams allow the rigger the opportunity to stock a variety of different length pipe to accommodate different loads," said Kozickie. "They must follow a matrix that will change the lifting capacity based upon the length of pipe being installed."
When ordering either style of device, it's best practice to request the correct device that is required for the job. Each one has limitations that make it the preferred choice to complete a required lift.
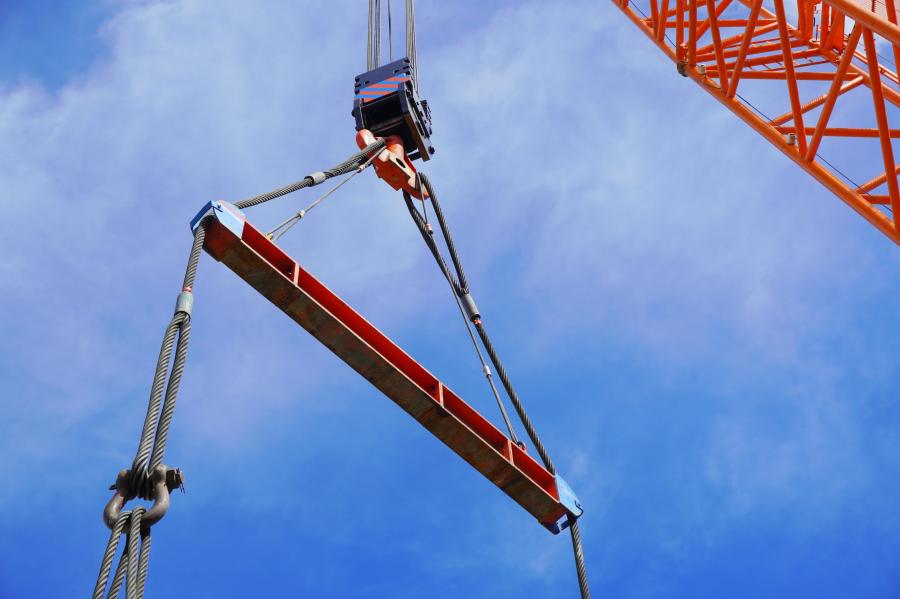
"Finally, verify that the beam is designed in accordance with the ASME B30.20-BTH-1 design criteria with the applicable design category and service class," Kozickie said. "The beam is also required to be proof tested to 125 percent of its rated capacity before placing it into service."
Spreader bars take on compressive stress in the beam as heavy loads are lifted, said HHI.
"It's a simple device — a long bar that holds two slings apart from each other."
The beam can either be attached to chain slings or synthetic slings at just the right angle, ensuring the right level of stress compression.
When using a spreader beam, a single crane can lift loads from multiple locations. This makes it a versatile device for companies without a wide range of cranes, said HHI.
These specific below-the-hook devices are used especially when lifting loads that might tip, slide or bend. They're also ideally designed to be used in preventing loads from being damaged. And they're perfect for efficiently lifting and moving wide or heavy-duty loads, said HHI.
Spreader bars are not designed for applications where there is minimal headroom, though, the company stressed. They should not be used if there is a possibility of load spinning, or if the load must be supported all the way through its length.
Working With Your Designer
These devices must be designed, manufactured and used according to ASME BTH-1 and B30.20 lifting standards. The ASME B30.20 volume specifies requirements for marking inspection, construction and operation of spreader bars and lifting beams, said Canadian engineering firm Basepoint.
The design must meet calculation requirements per BTH-1 to verify it will be safe and effective for the application.
"Using BTH-1, the failure modes of the beam will be addressed," said Basepoint founders Jason Thompson and Shawn Hansen.
This, though, is dependent on the intended use or classification of the beam.
The first step in developing a lifting device is determining the lifting configuration, maximum lifting capacity and maximum spread desired.
"We are looking at a beam that is lifted from the center and loaded at the ends," they said. "This type of lift subjects the beam to bending and shear," they noted, adding that bending stress and lateral torsional buckling are the primary modes of lifting beam failure.
Once the style and capacity of the lifting beam are determined, design category and service class must be confirmed, per ASME-BTH 1. These two factors establish the safety requirements for strength and fatigue in the remainder of the design calculations.
For lifting beams subject to flexure or bending, ASME BTH-1 includes calculations for maximum allowable bending stress. These calculations are based on beam geometry, material properties and lateral spacing between braces. Depending on the features of the lifting beam, additional calculations for connections (bolts, pins and welds) are specified.
"These connection calculations will determine the suitable sizing and spacing of each," said Thompson and Hansen. "Calculations for fatigue are also specified in the standard, dependent on the service class of the bar and bar geometry."
The lift capacity of a spreader beam is calculated based on the allowable stress and beam length and includes the weight of the beam. The allowable bending stress is calculated by BTH-1, and the lift capacity is calculated from the allowable bending stress. The bending calculations include bar weight, but do not account for shear stresses.
Still misunderstood, spreader bars and lifting beams are both used to transport loads with overhead lifts. But engineers stress, each device has its differences that influence its purpose and functionality at various job sites. CQ